Supply Chain Planning: What is it and how it works?
Supply chain planning is how businesses keep things moving smoothly from suppliers to customers. It ensures the right product reaches the right place, at the right time, without overspending.
In this dynamic and fast-paced environment, strategic planning is what separates resilient operations from reactive ones. At GoComet, we’ve seen how effective planning transforms day-to-day logistics into a competitive edge.
What is Supply Chain Planning?
Supply chain planning is all about ensuring the right product reaches the right place at the right time, while minimizing costs and maximizing efficiency. It’s the process businesses use to anticipate demand, allocate resources, and manage their operations effectively.
Think of it as the blueprint that keeps everything moving, from sourcing raw materials to delivering finished goods to customers. By combining data, strategy, and technology, supply chain planning helps businesses stay prepared for market changes and consumer needs.
How Does Supply Chain Planning Work?
At its core, supply chain planning involves forecasting, coordination, and optimization. It starts with demand forecasting, where businesses predict how much of a product their customers will need. Based on this, they allocate resources like inventory, labor, and production capacity. Tools like supply chain planning systems and demand planning software ensure this process is smooth and data-driven.
The planning doesn’t stop there. Businesses also coordinate with suppliers and logistics providers to ensure timely delivery. This coordination relies heavily on real-time visibility, tracking shipments and managing inventory levels to avoid bottlenecks. The result? A streamlined supply chain that minimizes delays and keeps customers happy.
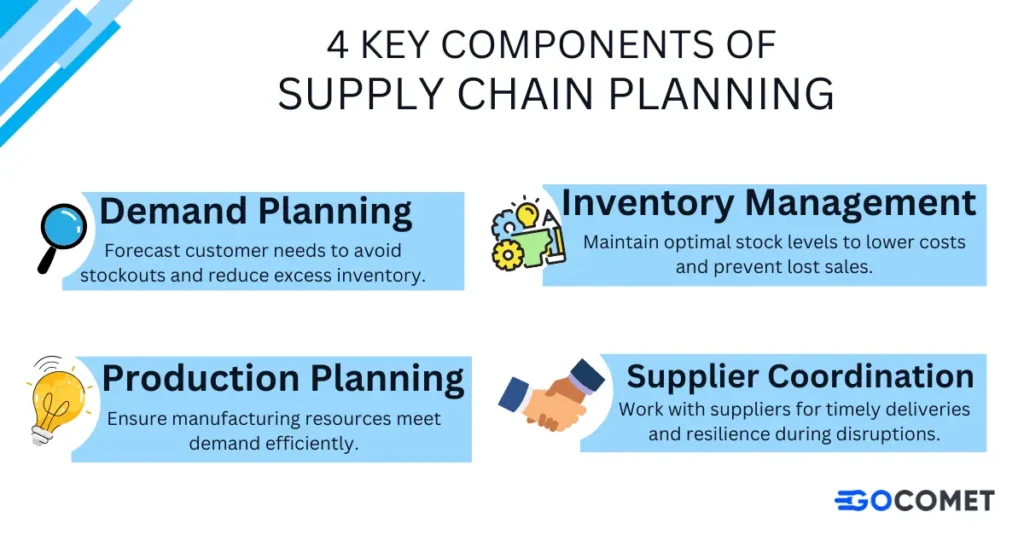
Benefits of Effective Supply Chain Planning
Supply chain planning is more than just about managing operations. It’s about creating a system that anticipates challenges and keeps everything running smoothly. We’ve worked with some of the largest global enterprises and seen how effective planning delivers measurable benefits first hand. Here’s what makes it so essential:
1. Lower Costs Across the Board
Planning is where cost efficiency begins. By forecasting demand accurately, businesses avoid overproducing or holding excess inventory. With the right tools, it’s easier to optimize transportation routes, reduce freight costs, and cut down on storage expenses, all without compromising on performance.
2. Better Customer Satisfaction
Meeting demand on time isn’t optional, it’s what builds trust. Supply chain planning ensures the right products are delivered at the right time, avoiding delays or shortages. This reliability not only satisfies customers but strengthens long-term relationships.
3. Optimized Resource Utilization
Every resource matters, from raw materials to warehouse space. With strategic planning, businesses can allocate resources effectively, avoiding bottlenecks or idle assets. The result? Maximum output with minimal waste.
4. Agility to Handle Change
Market fluctuations and unexpected disruptions are part of the game. Effective planning ensures businesses can adjust quickly, whether it’s scaling production during a demand surge or re-routing shipments due to unforeseen delays. Flexibility is what keeps supply chains resilient.
5. Real-Time Visibility
Visibility is critical for staying on top of operations. With real-time tracking and monitoring, businesses have a clear view of their supply chain, from production to delivery. This makes it easier to catch potential issues early and ensure everything stays on schedule.
6. Stronger Risk Management
Risks are inevitable, but proper planning makes them manageable. Whether it’s supplier delays or transportation challenges, identifying these risks in advance allows businesses to take proactive steps to mitigate their impact.
Strategic supply chain planning creates a system that isn’t just efficient but also adaptable to the unpredictable nature of global markets. This level of control and foresight is what every business needs to stay competitive and deliver consistent results.
Technological Tools in Supply Chain Planning
Gone are the days of relying on instinct and manual tracking. Today, technology runs the show in supply chain planning, and it’s changing the game in ways we couldn’t have imagined a decade ago. Here’s how the right tools are reshaping supply chains:
Supply Chain Planning Systems
Think of these as your command center. They pull together data from all corners of your supply chain, giving you real-time insights that make decision-making faster and smarter. Whether it’s fine-tuning inventory or planning production schedules, these systems keep everything humming along seamlessly.
1. AI and Machine Learning
Imagine a tool that can spot patterns you might miss or predict a surge in demand before it happens. That’s what AI does. By crunching historical data and monitoring trends, AI keeps you ahead of the curve. It’s not just about avoiding mistakes, it’s about being one step ahead, always.
2. Supply Chain Visibility Platforms
Ever wish you could see every shipment in transit, every inventory level, every bottleneck, all at once? Visibility platforms make that a reality. They let you track your supply chain like you’re watching a live map, so you can act fast when something goes off course.
3. ERP Systems
If supply chain planning is a puzzle, ERP systems are the glue that holds all the pieces together. They connect procurement, production, and logistics into one seamless workflow, eliminating communication gaps and making life a whole lot easier.
The best part? These tools don’t just fix problems, they prevent them. That’s the power of integrating technology into supply chain planning.
Common Challenges in Supply Chain Planning
Let’s be honest: supply chain planning isn’t all smooth sailing. It’s more like navigating a busy intersection during rush hour. Here are some of the biggest roadblocks businesses face and how to steer clear of them:
1. Demand Fluctuations
Ever tried to predict what customers want next month? It’s tricky. Overestimate demand, and you’re stuck with warehouses full of unsold stock. Underestimate it, and you risk running out just when your customers need you most.
2. Supplier Delays
Even the best-laid plans can fall apart if a supplier misses a delivery. Whether it’s raw materials or key components, delays can ripple through your entire supply chain, causing missed deadlines and unhappy customers.
3. Lack of Visibility
It’s hard to make good decisions when you don’t have the full picture. Without real-time visibility, it’s like trying to solve a puzzle with half the pieces missing.
4. Poor Communication
Ever played telephone as a kid? That’s what supply chains can feel like when teams or partners don’t communicate effectively. A simple miscommunication can turn into a major delay.
How to Overcome These Challenges
- Use Real-Time Data Tools: Platforms that provide live updates on shipments and inventory make it easier to spot and fix issues before they escalate.
- Build Strong Supplier Partnerships: Open communication and trust with suppliers go a long way in avoiding delays and resolving problems quickly.
- Empower Your Team with Training: The right tools are only as good as the people using them. Make sure your team knows how to leverage advanced planning systems.
- Plan for the Unexpected: From demand surges to supplier setbacks, having a Plan B (and C) can save the day.
Supply chain planning might come with challenges, but with the right approach, they become manageable hurdles instead of roadblocks.
Strategies for Supply Chain Planning
Supply chain planning isn’t a one-size-fits-all deal. It’s a blend of art and science, getting the basics right while leaving room for creativity and innovation. So, what strategies actually work?
1. Let Data Lead the Way
Guessing isn’t planning. The smartest supply chains are data-driven. By analyzing trends and historical data, businesses can make decisions that aren’t just accurate, they’re spot on.
2. Start with the Customer
Your supply chain doesn’t exist in a bubble. It’s there to serve your customers. Planning with their needs in mind, whether that’s faster delivery or greater product availability, keeps you competitive.
3. Make Visibility Non-Negotiable
Without visibility, you’re essentially running blind. End-to-end tracking tools ensure you know what’s happening at every stage of your supply chain, helping you spot inefficiencies and avoid surprises.
4. Think Green
Sustainability isn’t just about being eco-friendly, it’s about being efficient. Reducing waste and optimizing logistics not only saves money but also meets growing customer demand for greener practices.
5. Keep Evolving
A good plan today won’t necessarily work tomorrow. Continuous improvement, whether it’s adopting new technology or revisiting old processes, is what separates the best supply chains from the rest.
These strategies aren’t just theory, they’re what keeps supply chains efficient, flexible, and ready for anything.
Also Read: What does Green Supply Chain Management mean?
Future Trends in Supply Chain Planning
What’s next for supply chain planning? The future is exciting, but it’s also demanding. Here’s a glimpse of what’s on the horizon:
1. AI-Driven Everything
AI isn’t just a nice-to-have anymore, it’s becoming the standard. From predictive analytics to real-time optimization, AI is turning supply chains into intelligent, self-improving systems.
2. Blockchain for Transparency
Blockchain isn’t just for cryptocurrency. It’s transforming supply chains by offering a secure, tamper-proof way to track every transaction. That means fewer disputes, greater accountability, and better trust between partners.
3. Digital Twins
Imagine testing changes in a virtual copy of your supply chain before rolling them out in real life. That’s what digital twins allow businesses to do, spot risks, optimize processes, and make smarter decisions.
4. Sustainability as Strategy
Sustainability isn’t just an add-on anymore, it’s becoming central to supply chain planning. From reducing carbon footprints to adopting circular logistics, businesses are rethinking their entire approach to align with environmental goals.
5. Collaboration Over Competition
Future supply chains will focus more on partnerships. Whether it’s working closely with suppliers or logistics providers, collaborative planning will drive efficiency and innovation.
Keeping an eye on these trends isn’t just about staying relevant, it’s about staying ahead. The supply chains of the future will belong to those who adapt and innovate.
Conclusion
Supply chain planning is the glue that holds every operation together. From forecasting demand to optimizing resources and navigating challenges, it’s the backbone of any efficient and resilient business. We’ve explored its key components, the tools that make it possible, and strategies to ensure success. Whether it’s embracing real-time visibility, leveraging AI, or planning for future trends like sustainability and digital twins, supply chain planning is evolving at an incredible pace.
But here’s the thing, planning isn’t just about getting things right today. It’s about staying ready for tomorrow. Markets shift, technology advances, and customer expectations grow. The real question isn’t what your supply chain can do right now. It’s how it’s preparing you for the next challenge or opportunity.
Ready to make your supply chain future-proof? It starts with the next step. What’s yours?
FAQ
What tools are essential for effective supply chain planning?
Key tools include supply chain planning systems, demand forecasting software, real-time visibility platforms, and ERP systems. These tools streamline operations, enhance decision-making, and improve efficiency across the supply chain.
How does supply chain planning differ from logistics management?
Supply chain planning focuses on forecasting, resource allocation, and optimizing the flow of goods, while logistics management deals with the physical movement and storage of goods. Together, they ensure a smooth and efficient supply chain.
Why is demand forecasting critical in supply chain planning?
Demand forecasting helps predict customer needs accurately, ensuring businesses produce and deliver the right quantities. It minimizes waste, reduces costs, and prevents stockouts or overproduction.
What are the objectives of supply chain planning?
The primary objectives include aligning supply with demand, reducing costs, improving efficiency, and ensuring customer satisfaction. Effective planning creates a streamlined process that adapts to market changes.
What is the difference between supply chain planning and supply chain execution?
Supply chain planning involves forecasting, strategizing, and allocating resources before execution. Supply chain execution focuses on implementing those plans, such as coordinating logistics and managing inventory in real-time.
What are the steps involved in the supply chain planning process?
The steps include demand forecasting, inventory management, production planning, logistics coordination, and supplier collaboration. Each step ensures the supply chain runs smoothly and meets customer needs.
How do supply chain planning systems optimize processes?
These systems integrate data from across the supply chain to provide real-time insights. They help businesses forecast demand, manage inventory, schedule production, and coordinate logistics efficiently.
What is supply chain strategic planning?
Strategic planning focuses on the long-term goals of the supply chain, such as cost reduction, scalability, and sustainability. It involves aligning supply chain activities with the overall business strategy to drive growth.
What are the benefits of supply chain planning for consumer goods?
For consumer goods, supply chain planning ensures consistent product availability, reduces costs and improves customer satisfaction. It also helps manage seasonal demand and respond quickly to market changes.
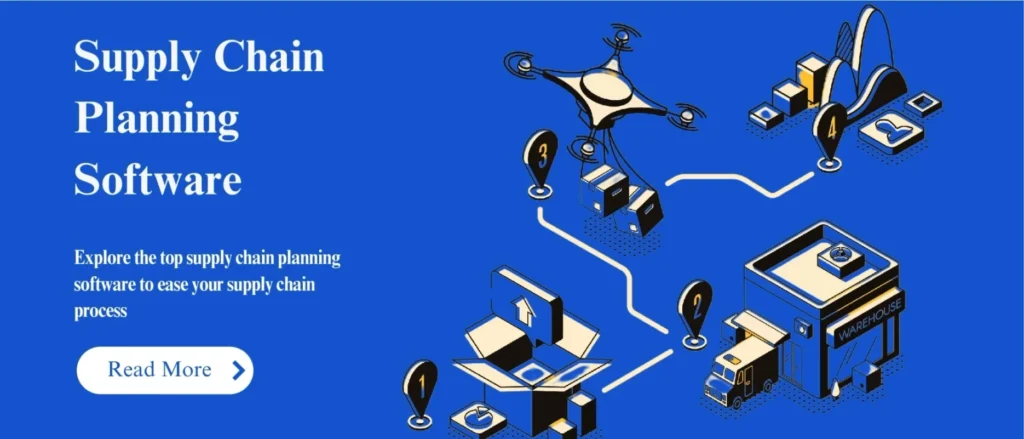